DUO
Constant pressure self-cleaning filter system
Suitable for highly contaminated materials
Constant pressure operation
DUO | Filtering surface area [cm2] | Heating zones | Max pressure [bar] | Maxfì flow rate [kg/h]1 | Filtration [µm] |
---|---|---|---|---|---|
1400 DS | 1418 | 7 | 350 | 2000 | 60-2000 |
1750 DS | 1756 | 7 | 350 | 3000 | 60-2000 |
1750 DS Auto | 1756 | 7 | 350 | 3000 | 60-2000 |
2800 DS | 2847 | 7 | 350 | 5000 | 60-2000 |
3500 DS | 3515 | 7 | 350 | 6000 | 60-2000 |
5600 DS Twin | 5694 | 14 | 350 | 10.000 | 60-2000 |
7000 DS Twin | 7030 | 14 | 350 | 12.000 | 60-2000 |
(1)The flow rate depends on various factors: melt viscosity, filtration finess, type and percentage of contaminant, production line. |
Break Machinery DUO videos
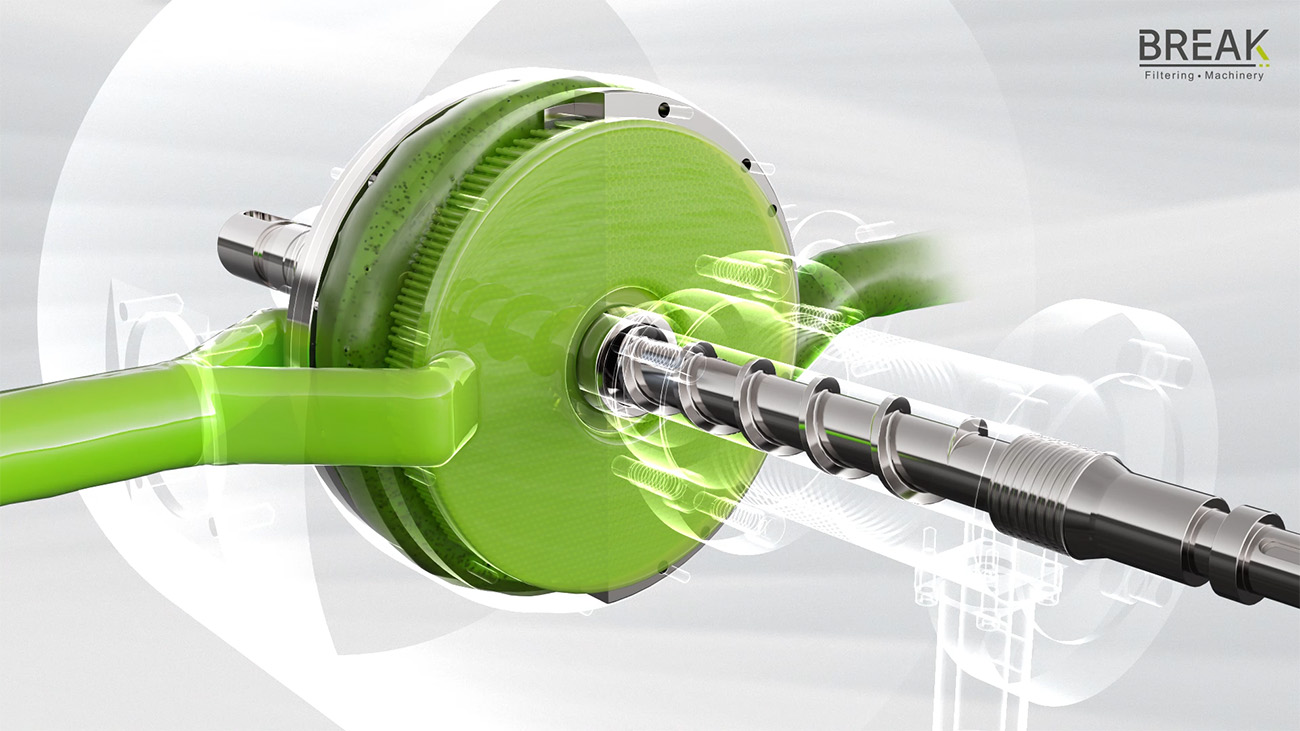
Break Machinery DUO video
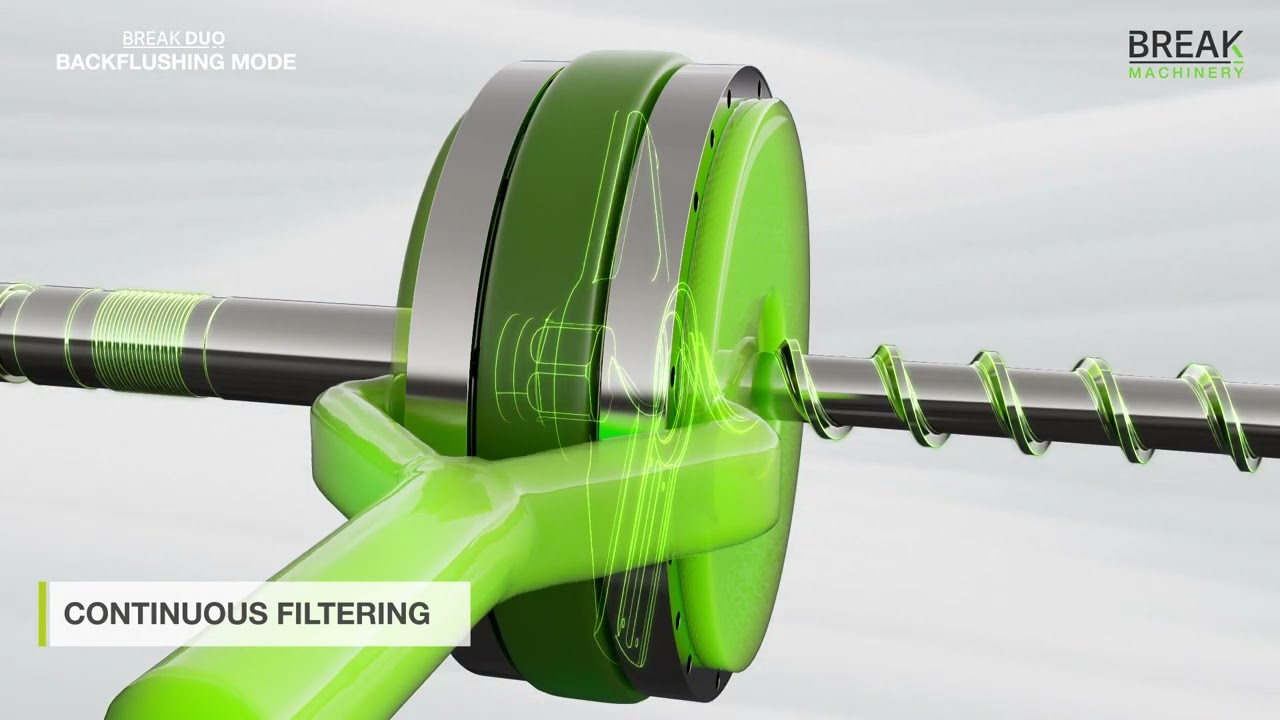
Break DUO backflushing system video
Technical features
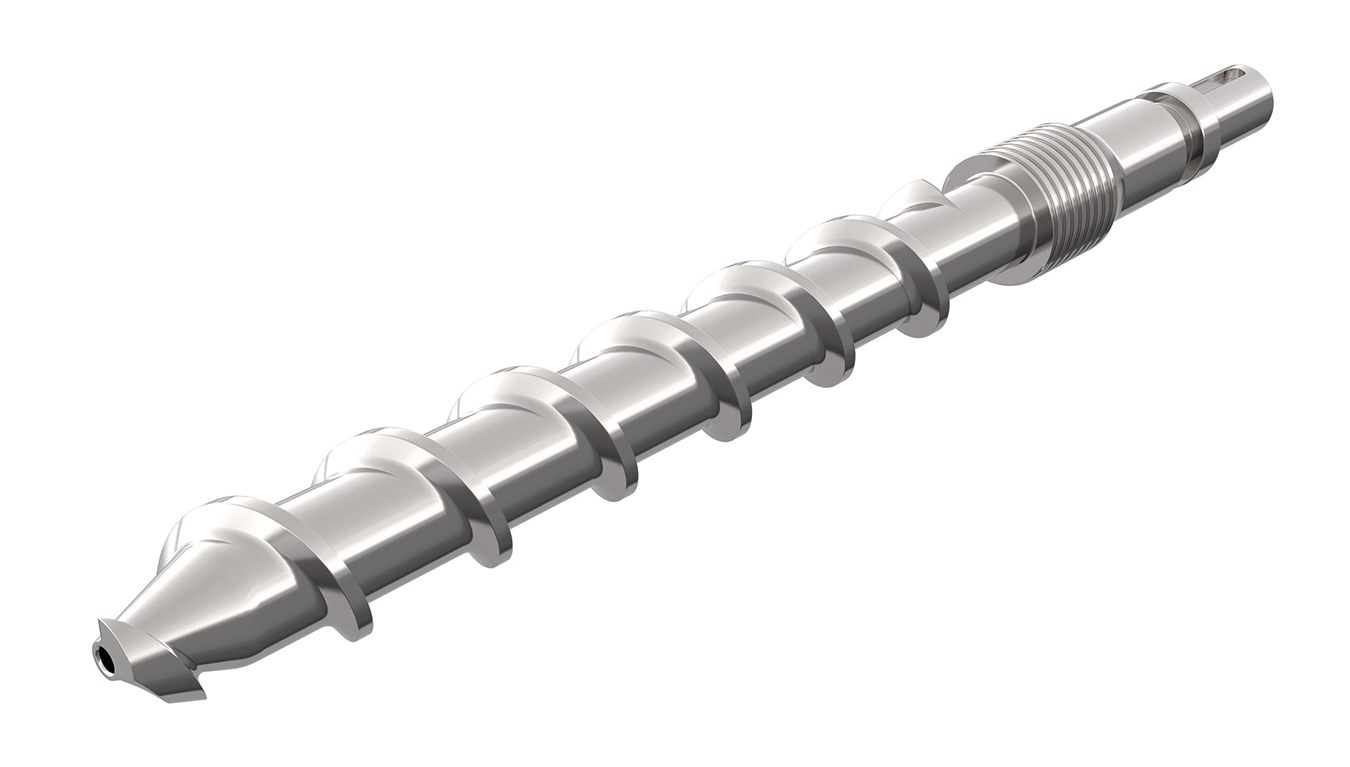
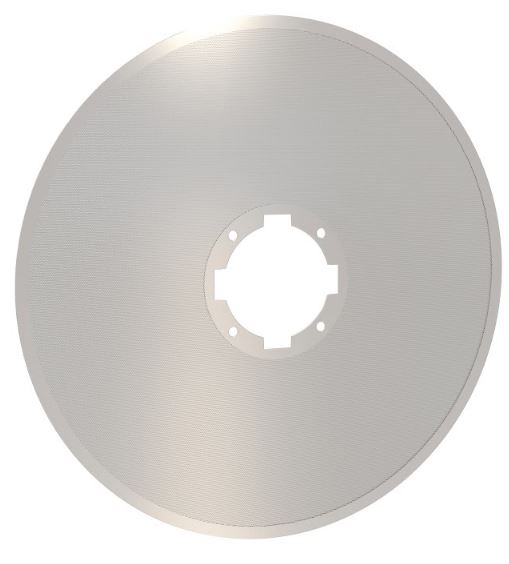
Its design also prevents contaminants filtrates from re-entering the melt.
Continuous cleaning allows to use filters longer than traditional technologies.
The conical shape of the holes helps the plastic to go through them.
Economic Advantages
The presence of the operator is reduced considerably.
Standard and special maintenance operations are simple, fast and can be carried out directly at the customer’s production site.
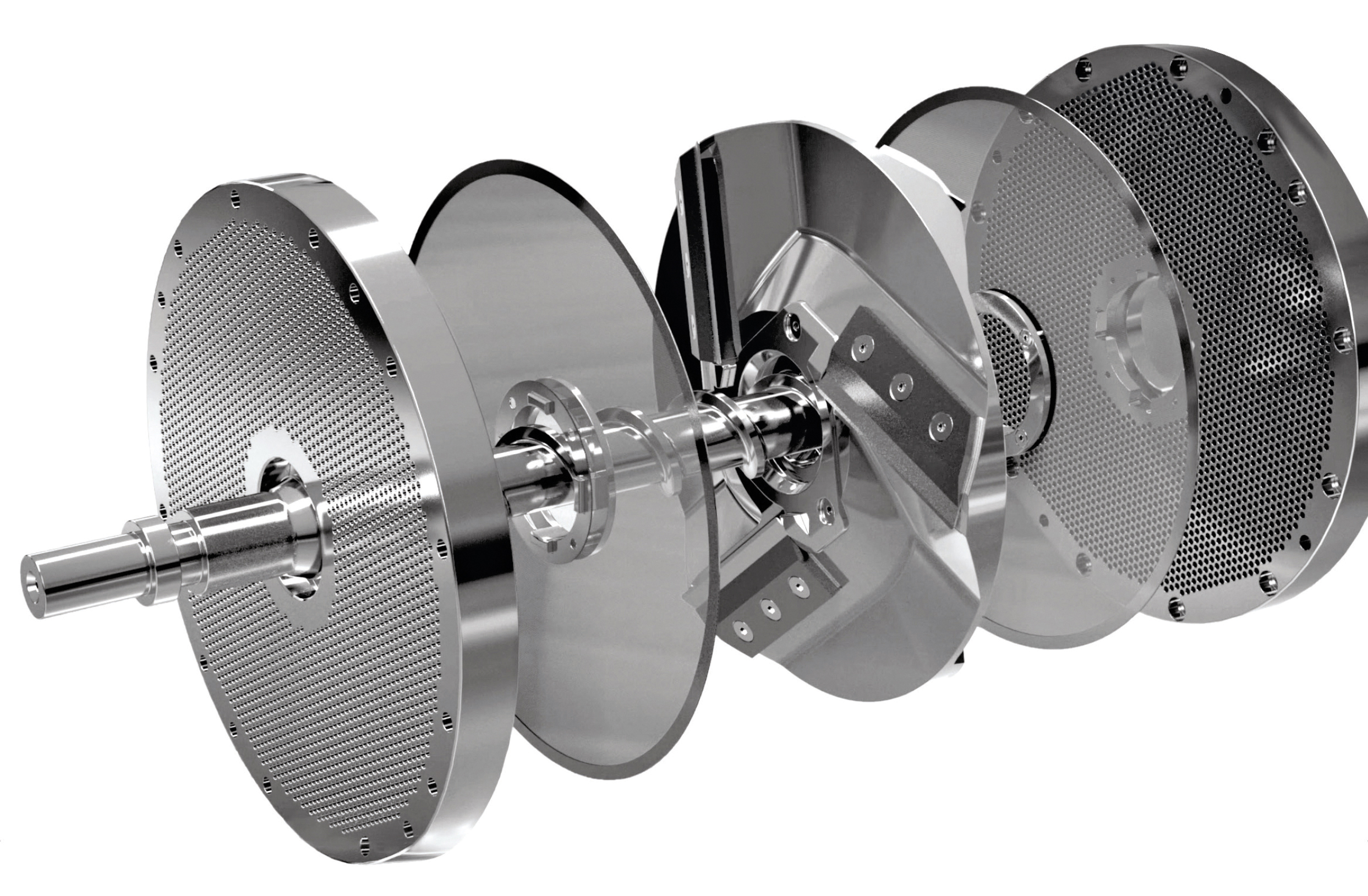
Scraping operation
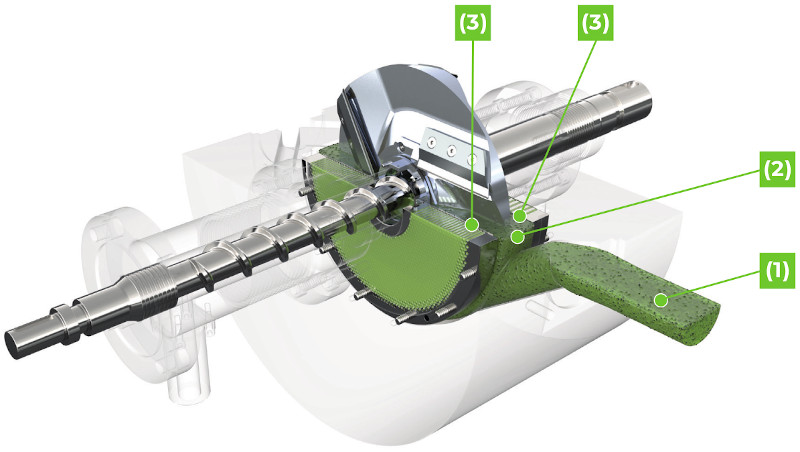
The melted plastic material (1) is conveyed into the filtration chamber (2) and passes through two filters (3) facing each other.
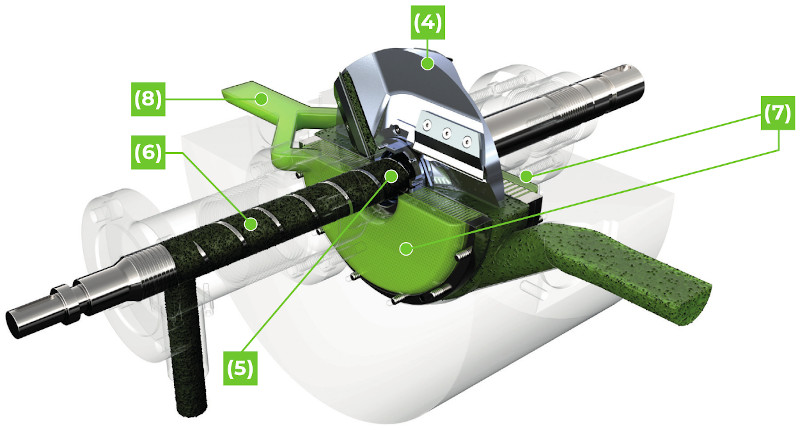
The centre of the scraper disc is in communication with an independent discharge screw (6) that expels the contaminated material.
The melted plastic material filtered (7) from the two filters then rejoins the outlet channel (8) to pass on to the next process.
DUO 5600 and 7000 Twin: continuous production
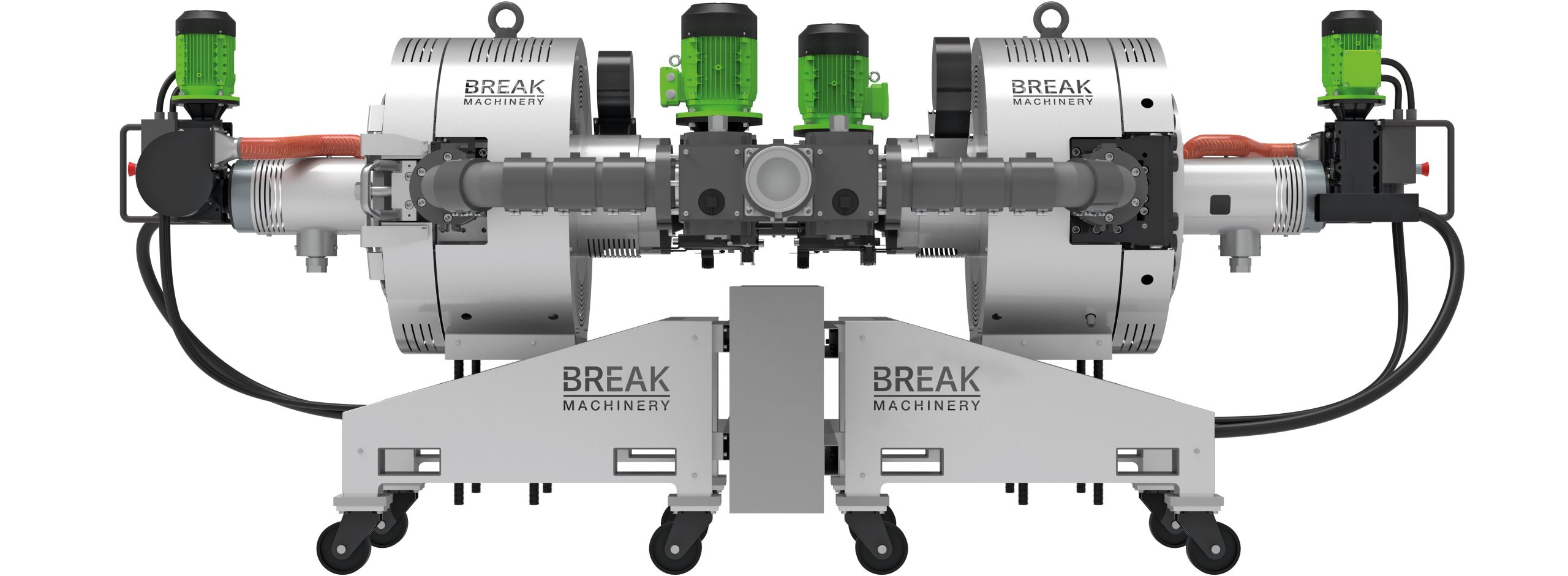
DUO | Filtering surface area [cm2] | Heating zones | Max pressure [bar] | Maxfì flow rate [kg/h]1 | Filtration [µm] |
---|---|---|---|---|---|
5600 DS Twin | 5694 | 14 | 350 | 10.000 | 60-2000 |
7000 DS Twin | 7030 | 14 | 350 | 12.000 | 60-2000 |
(1)The flow rate depends on various factors: melt viscosity, filtration finess, type and percentage of contaminant, production line. |
In this way, production is not interrupted and the screen can be changed, without having to stop the line. The same process is then carried out for changing the screen in the second machine.
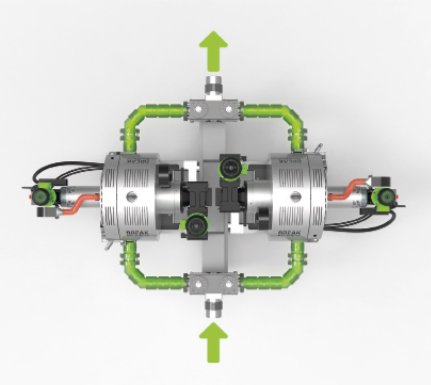
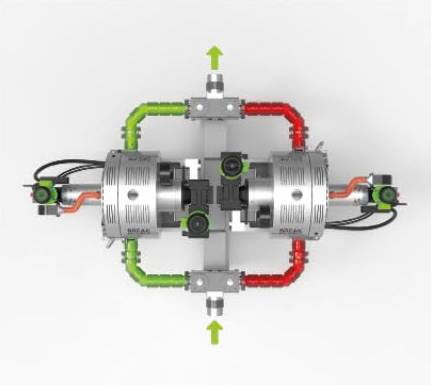
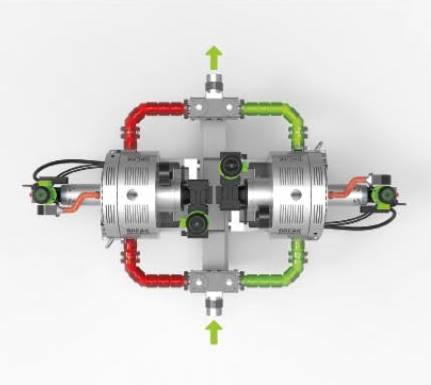
Automatic opening system
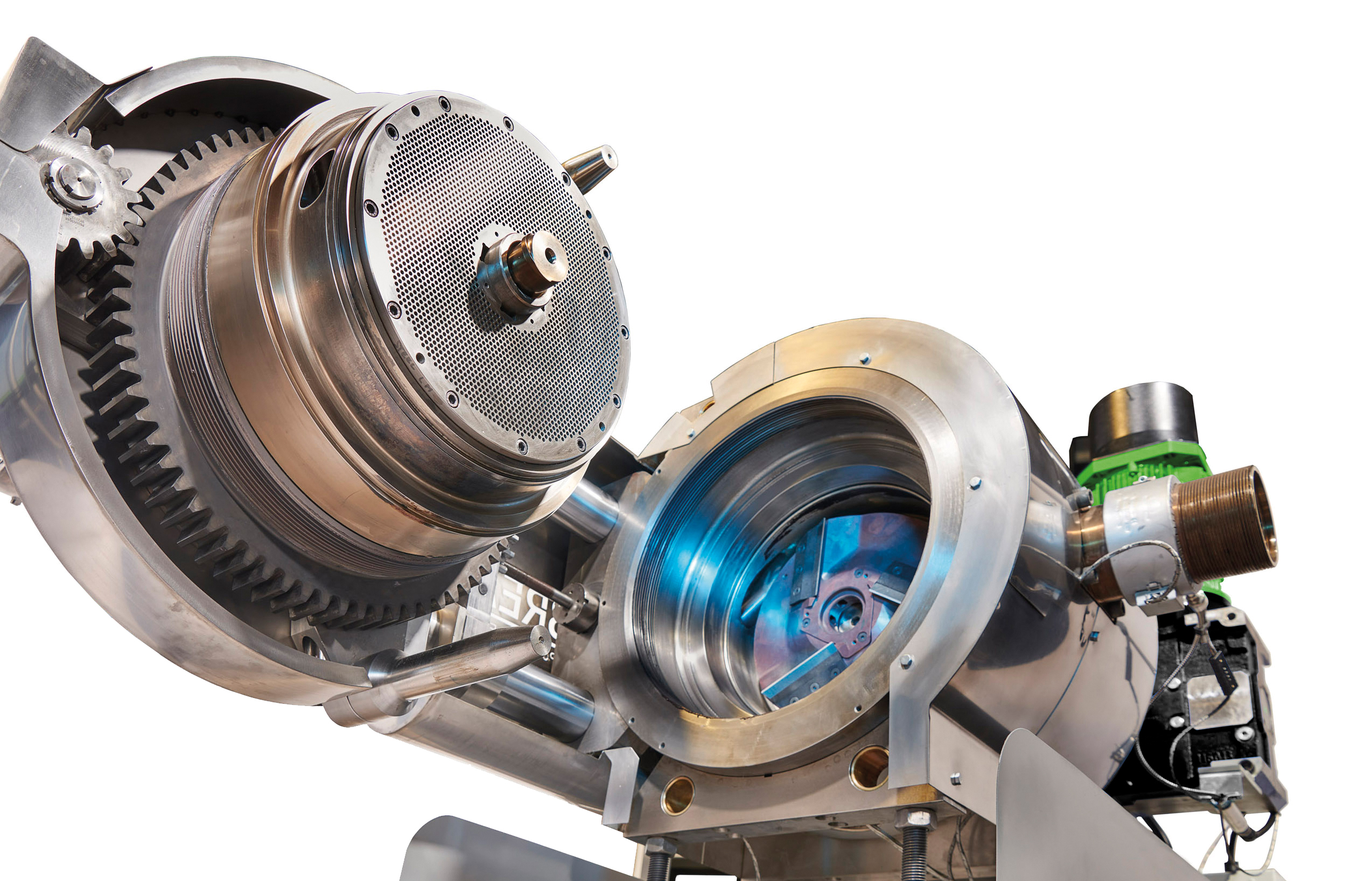
This system consists of a threaded lid that screws directly onto the machine body, and by a drive which controls both the screwing and the translation of the cover.
These two movements occur simultaneously thanks to a mechanism and a special clutch that allows the screw and nut to couple during the closing phase.
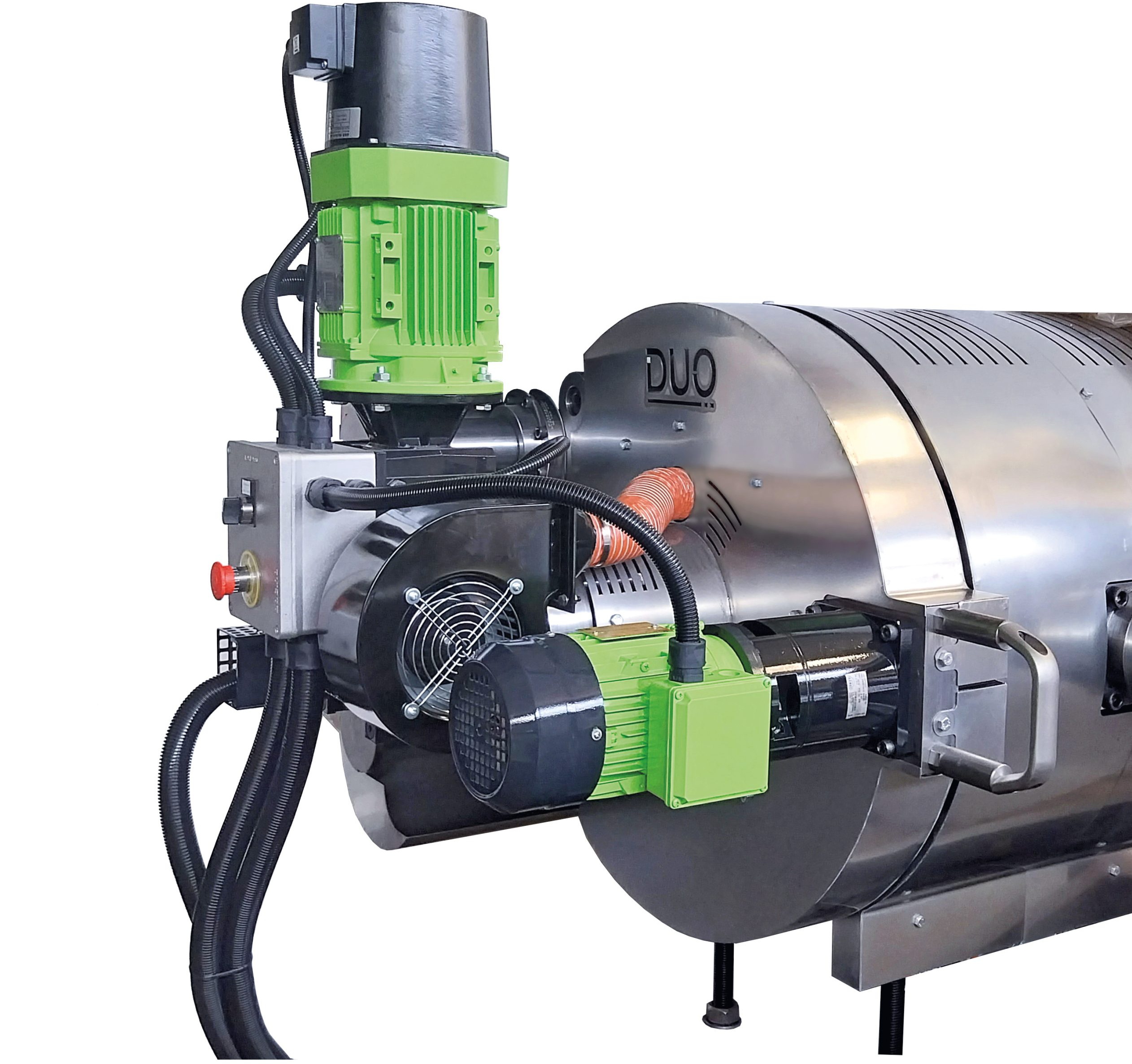
With this system the time required to open and close the cover is reduced, as it is no longer necessary to loosen and tighten the bolts manually; the operator’s work is therefore easier and much safer.
Back-flushing operation
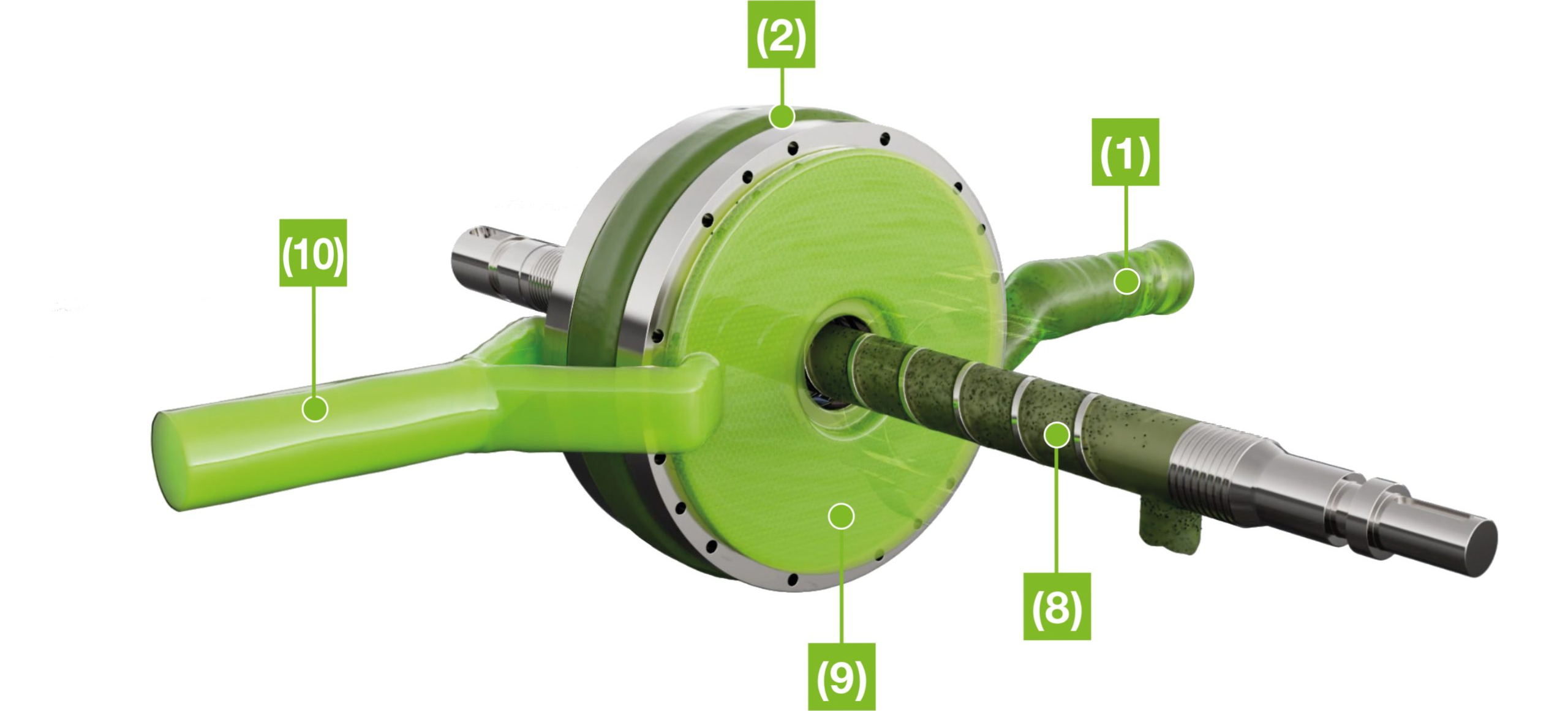
Each machine can switch from scraping mode to back-flush mode simply by changing the kit of internal components.
Furthermore, in case of, back-flush no laser or punched filters are necessary anymore.
Only metallic mesh filter.
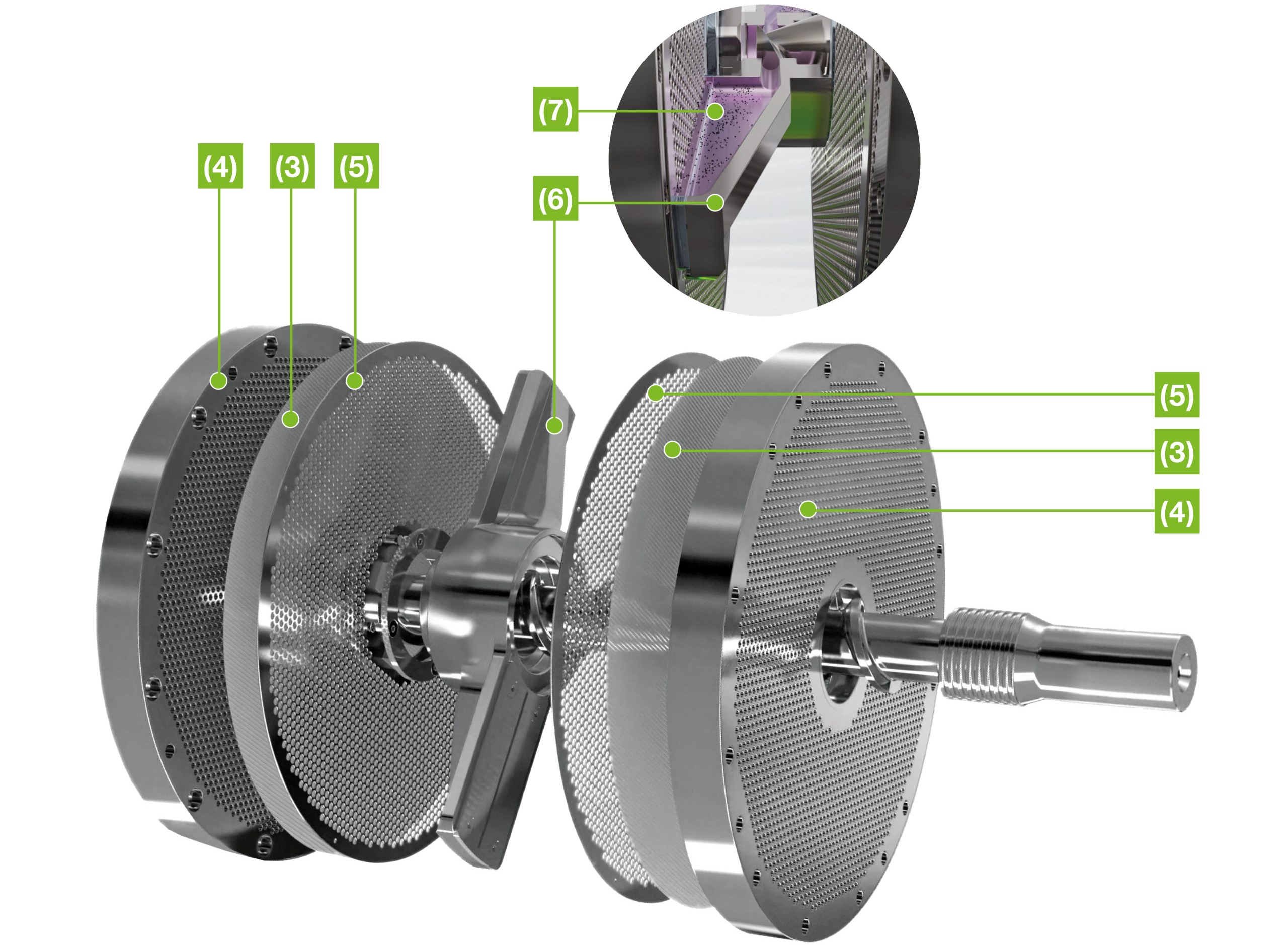
Supporting the two protective breakers is a cleaner (6) which sucks up the contamination (7) settled on the metal mesh.
The centre of the cleaner is in communication with an independent discharge screw (8) that ejects the contaminated material.
The filtered melted material (9) then rejoins into the outlet channel (10) to pass to the next process.
REQUEST INFORMATION
Our sales and technical department are at your disposal for advice and to give you all the necessary information on the filters that best suit your needs.