ONE and DUO screens: find the best fit
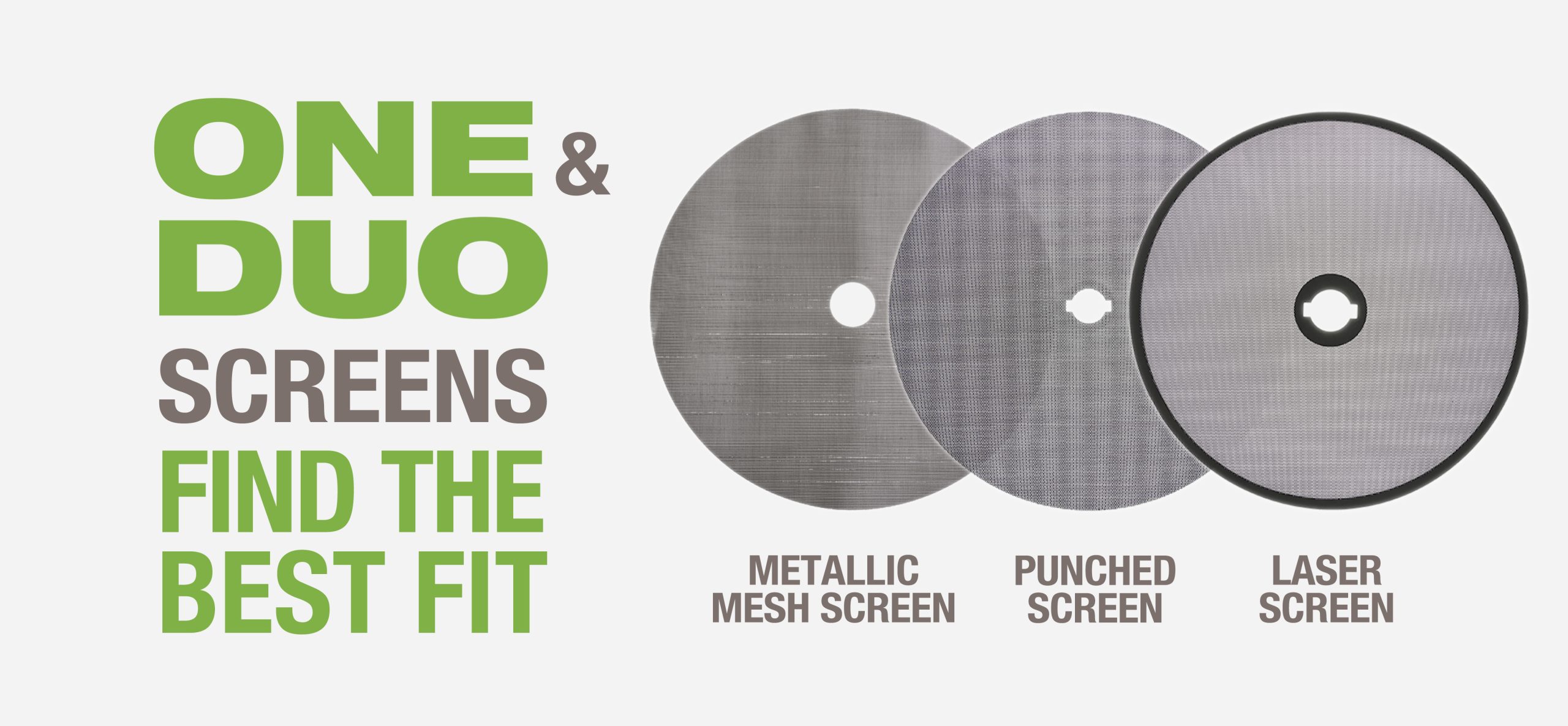
ONE and DUO support multiple screen types, allowing you to choose the configuration that best fits your production needs.
ONE and DUO are designed to work with a variety of screen types, each tailored to different contamination levels and filtration needs. Choosing the right screen is essential for maximizing efficiency, maintaining product quality, and reducing operational downtime.
Each screen type offers unique advantages in durability, precision, and cleaning capabilities, making them suitable for different industrial applications.
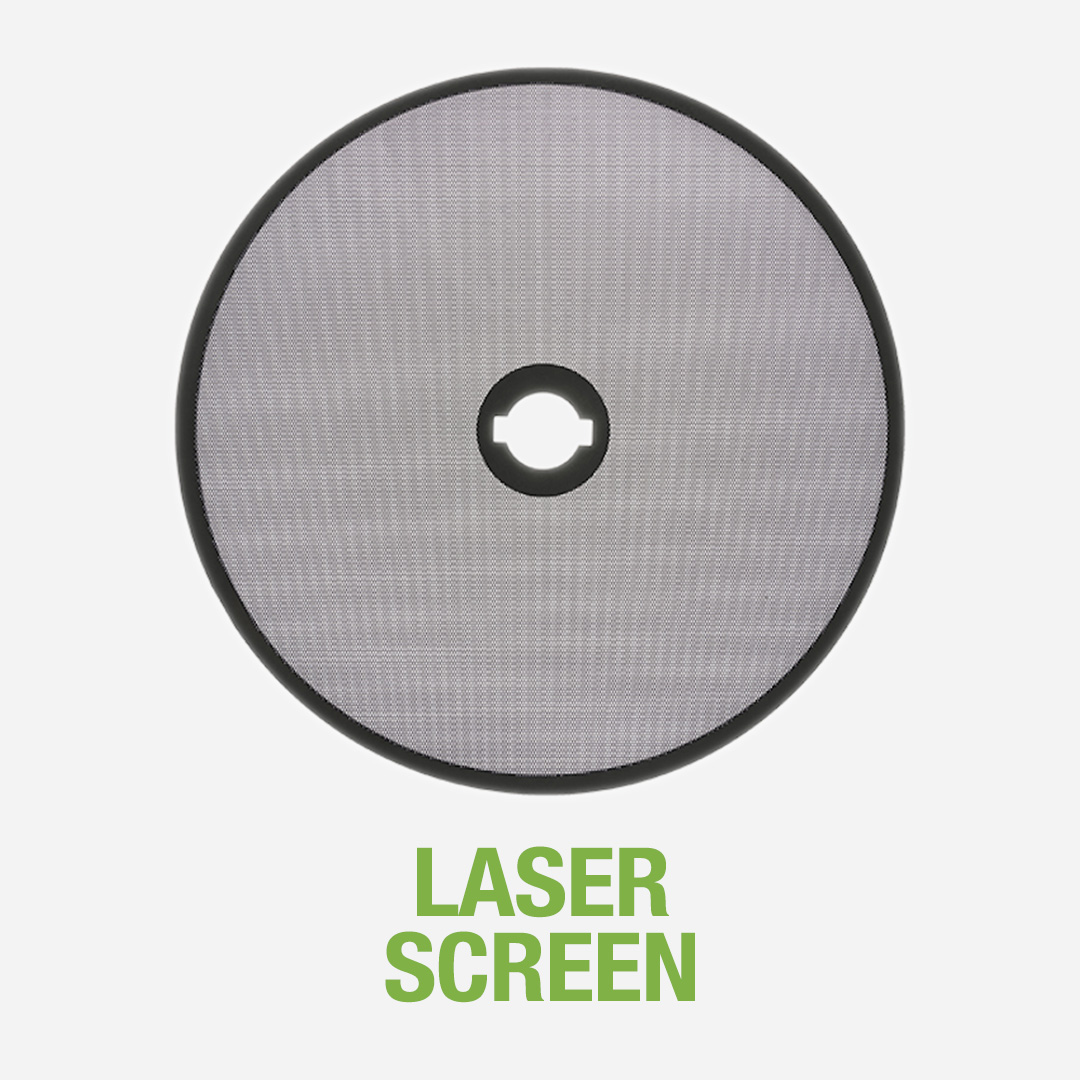
Application: Designed for fine filtration of materials with high purity requirements.
Advantages:
- Precisely remove small impurities to maintain material quality,
- Treated for wear resistance and high-temperature durability,
- Can be cleaned in a pyrolytic oven for reuse, reducing waste and maintenance costs.
Best for: Fine particle separation in high-quality recycled plastics, polymer production, and chemical processing.
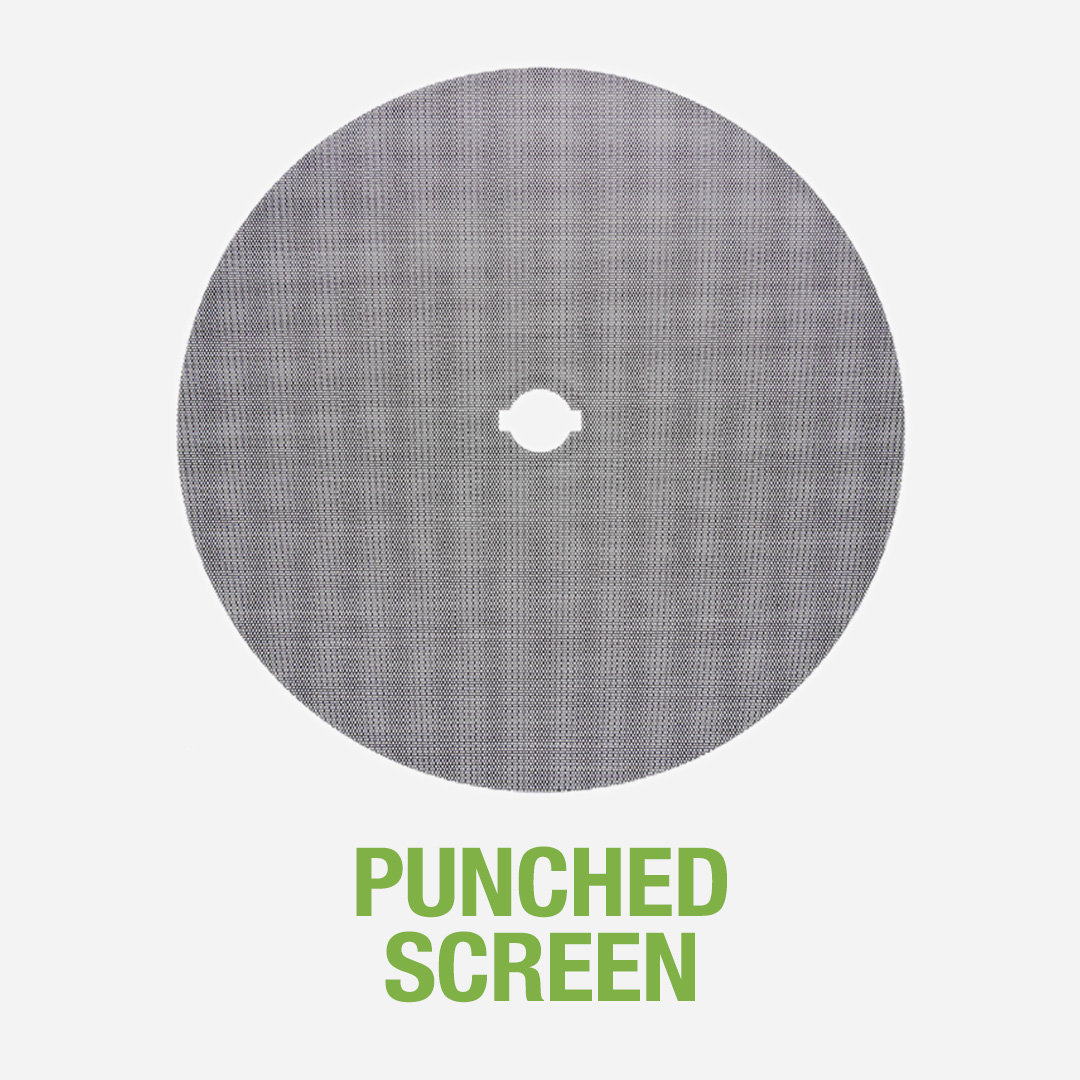
Application: Used for coarser filtration where larger impurities need to be separated.
Advantages:
- High mechanical resistance to handle large contaminants without damage,
- Durable under high-load operations, extending lifespan,
- Can be cleaned in a pyrolytic oven for reuse, reducing waste and maintenance costs.
Best for: Processing heavily contaminated materials with large impurities.
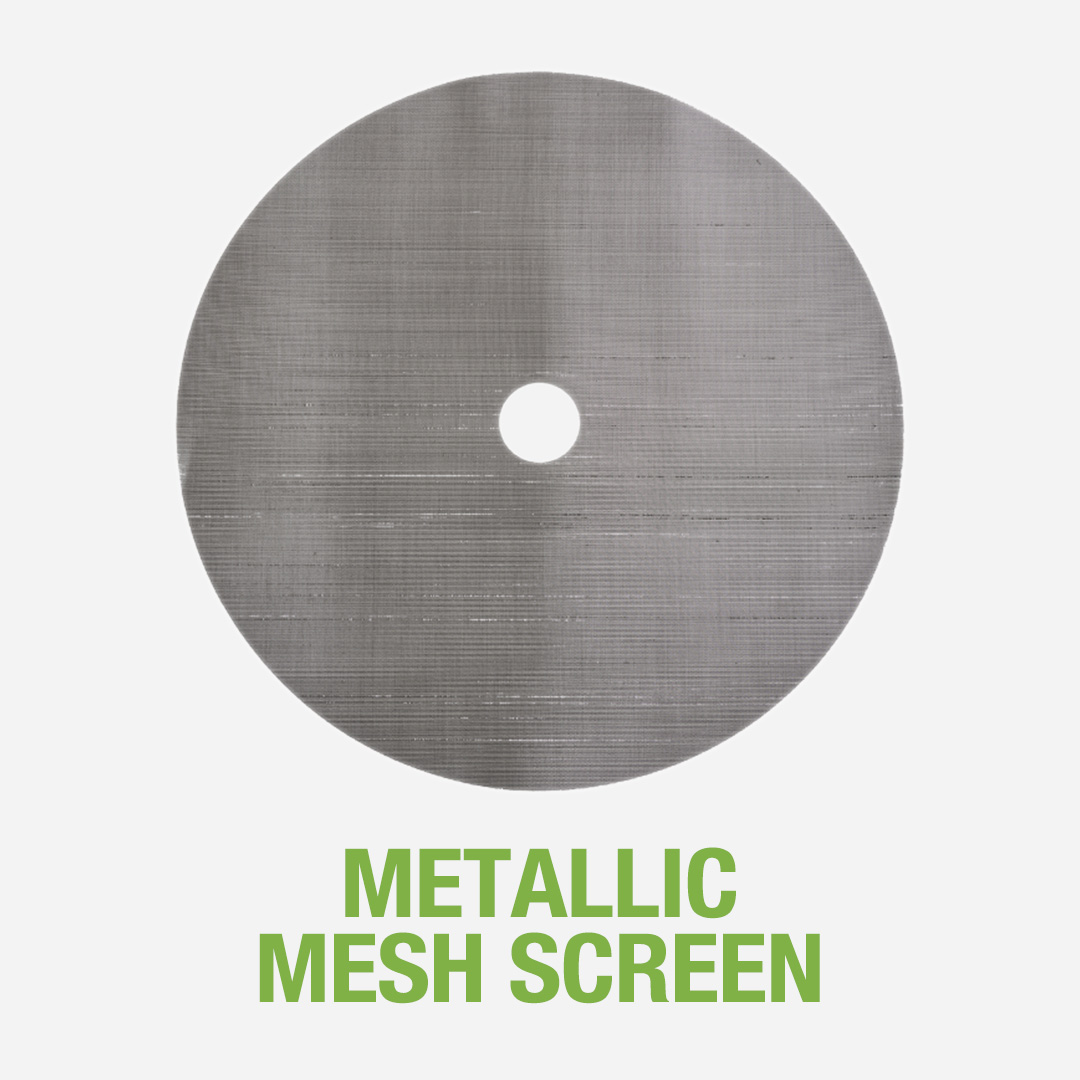
Application: Used in backflushing cleaning systems for lightly contaminated materials.
Advantages:
- Economical and efficient for low-contamination applications,
- Provides reliable filtration while minimizing maintenance costs.
Best for: Continuous filtration where cost-effectiveness and efficiency are key.
To learn more about ONE and DUO screen configurations, email Alessandro Sartori at
alessandro.sartori@breakmachinery.com